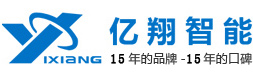
高光无痕模具、高光塑料材料和急冷急热控制管理系统是高光无痕注塑成型技术的三个主体组成部分,其中高光无痕模具是该技术的关键和核心部分。
高光无痕模具是一种以高温蒸汽作为加热介质,通过急冷急热控制管理系统控制模具的温度,辅以热流道、电磁阀及时序控制器分时进胶的模具。
高光无痕模具主要特征:第一,模具成型温度比较高。在较高的模温下注塑成型有利于消除熔接痕、流痕、产品内应力等缺陷。因此模具在工作时需加热,为避免热量损失,通常都会在定模侧加树脂隔热板;第二,模腔表面极度光亮(一般为镜面2级或更高)。高光模具生产出的产品能直接用于装配整机,无需做任何表面处理,因此这种工艺对模具钢材及塑胶材料的要求都很高;第三,热流道系统的热嘴较多(一般为6~8个嘴,有时会更多)。每个热嘴必须带封针且有独立的气道,通过电磁阀及时序控制器等进行单独控制,实现分时进胶,进而达到控制,甚至消除熔接痕。
同高压水温机作用原理相似,模具内部设计均衡的管道,加热时通人蒸汽,冷却时切换为低温水,实现模具表面的加热或冷却(蒸汽加热前一般还需要用压缩空气将管道吹干)。高温度高压力蒸汽加热系统可使模具表面最高温度达到160℃。由于蒸汽相对于水,其热容较小,相对升温时间比较久。达到150℃模具表面温度需要300℃左右的蒸汽。但由于生产的全部过程中蒸汽不可循环利用,要安设锅炉设备和铺设管道等,致使其运行成本偏高。
高光无痕注塑成型的过程:合模→输入高温水蒸汽→注塑→排出水蒸汽→投入冷却水(冷却)→清除冷却水(用高压空气清洁)→开模→顶出→型合。
在高模温条件下,当模温高于成型材料的热变形温度时,可以使成型材料拥有高光泽度。同时,高光无痕注塑成型技术还消除了传统注塑成型工艺存在的熔接痕问题,并能免去产品二次加工的必要,能节约成本(例如:喷漆),环保节能。另外,普通的注塑成型技术,在加入GF(GlassFiber,玻璃纤维)、CF(CarbonFiber,碳纤维)、MF(MetalFiber,金属纤维)后,可以加强产品的性能,但外观不是很好,而采用高光无痕注塑成型技术,由于模具表面高温,加入的GF、CF、MF能进入产品聚合物的内部,使成型材料表面结晶比率增加,表面效果很好,并对提升产品表面硬度有一定帮助。
高光无痕注塑成型技术对模具有一些基础要求:模具内表面要求非常高的光洁度,以确保制品的表面上的质量。模具内部开设管道必须合理,以确保能够迅速升温和降温。模具内部的管道应该导热性能好。由于生产的全部过程中需要不停加温及降温,模具需选用高质量的钢材。在使用的过程中要尤其注重模具的保养,确保干燥,无尘。
另外,高光无痕模具的性能和寿命与模具所使用的钢材有着直接的关系,塑胶模具零件由于其工作条件不同,受外部影响情况也不相同,因此,对钢材除了基本要求外,还要有所侧重。例如大型高光塑胶模具型腔用钢材,除了要求拥有非常良好的切削性、放电加工性和焊接性能外,还需要具有极佳的抛旋旋光性和较高的硬度等特点。这不但可以成型出表面光亮美观的产品,又能减小塑料对型腔表面的磨损,既延长了模具常规使用的寿命,又降低了注塑压力,保护了注塑机。目前平板电视不同工艺设备加工条件使用的高性能高光无痕模具钢材有POLMAX、LKM838H、LKM818H、S-STAR(A)、NAK80、STAVAXS136、STAVAXS136H、OPTIMAX、X13T6W(236)、X13T6W(236H)等。(end)
电磁感应加热是根据法拉第电磁感应原理加热模具的表面温度。交变磁场产生的感应电流具有集肤效应,涡流分布模具表面而芯部接近于零。因此,电磁感应加热只在模具表面至集肤深度范围加热,加热体积小,升温速度快,台湾中原大学研发的系统升温速度可到40℃/s以上。
(6)红外线辐射加热系统研究人员正开发利用红外线辐射的方式直接对型腔部位加热。红外线的传热形式是辐射传热,由电磁波传递能量,不需要传热介质,具有一定的穿透能力。与其它方式相比,具有节省能源、安全、设备简单、易推广等优点。但由于光亮金属烈J红夕卜线吸收能力较弱,加热速度慢。
高温气体作为快速变模温的介质,在充填阶段前快速准确确定量地将气体注入型腔中,可以瞬间将模面温度提高至200℃左右,且高温区域可控制在模具表面附近,不会造成模具其它部分因温度京华剧烈产生尺寸膨胀的配合度问题。该技术无需对现有模具作太大的修改,模具制造成本较低,但密封要求高。
(1)改善制品外观品质,有效消除产品表面熔接痕、银纹、表面浮纤等注射成型缺陷。
采用快变模温技术,模腔表面温度被快速提升至树脂塑料的热变形温度以上,从而增加熔融塑料在模腔内的流动性,降低熔融塑料与模腔表面之间的磨擦阻力,显着消除制品表面熔接痕、银纹等外观缺陷。同时,经过控制模腔表面加热和冷却的时间变化可改变塑料制品表面的结晶状态,有效消除因玻纤外露于产品表面影响外观的问题。
模具内部设计均匀的加热或冷却管道,通过油加热系统达到模具预热的功效,同时在注射过程有冷却的作用。最高温度可达350℃。由于油的热传导系数低,效率较低,而且产生的油气影响高光成型质量,但效果比较不理想。但目前企业油温机比较普遍,使用经验丰富。
模具内部设计均衡的管道,不同阶段使用不相同温度的水。加热时通人高温过热水水,冷却时切换为低温冷却水,实现模具表面的加热或冷却。如将水加压,温升还可达140~180℃,升温很快。高温度高压力的水温控制管理系统的制造厂商有:如奥德的GWS系统,由于热水可循环利用,运行成本较低,是目前国内市场上使用较多的一种,也是代替蒸汽的最佳选择。
高光无痕注塑成型技术又称快速模具的温度加热冷却成型技术RHCM(Rapid Heat Cycle Molding)。这种成型工艺主要是在注塑成形时通入高温蒸汽,瞬间把模具的温度上升为100~150℃,同时,为了更好的提高生产效率,在模具高温加热后,模具表面应迅速冷却为20~40℃。
快变模温技术提供的高模温除了可提高熔体的流动性、减小注射压力,还能够更好的降低注射速率和熔体充模过程中受到的剪切力,减小最终成形塑件的残余应力和翘曲变形,改善制品结构性能。
快变模温技术可提升产品表面光洁度,表面光洁度可达到镜面要求;无需对环境造成污染的喷漆等後续加工,大大降低成本,缩短制品的成型周期。
高光注塑是目前注塑企业最为通用的叫法,从注塑产品的光泽上看,由于熔体流动前沿与模面接触点的界面温度提高,可使模具部分的微细形状复制容易,如结合表面高光的模具、特殊工程塑料,可生产出高光泽度的注塑产品,实现一步注塑成功最终产品,由此被称为高光注塑,其全称应该为高光产品的变模温注塑。除此之外还有其它很多叫法,比如:该工艺采取了快速加热冷却,被称为快速热循注塑(RHCM);从模具的温度变化来看,称为变模温、动态模温、交替冷热模温控制技术;从消除喷涂等后处理工序看,被称为免喷涂注塑;从消除表面缺陷上看,称为无熔接痕、无痕注塑。从加热方式分,又称为蒸汽式、电热式、热水式、高油温式、感应加热式模温控制技术等。从模温控制机看,又称为蒸汽模温机、过热水模温机、电热模温机、水温机、油温机、电磁感应模温机等。(end)
优缺点:采用蒸汽加热,模具的温度控制精度高,加热及冷却范围大,可获得表面光亮、无熔接痕、无流痕、不需喷涂加工、塑件性能好、生产所带来的成本低的塑件。但由于增加了外在的蒸汽热源及模具内部开设的蒸汽管孔,系统较复杂,运行成本较高。
在快变模温控制过程中,冷热流体交替通入模具之中,实现更高品质的产品成型。
蒸汽加热是利用模温控制装置将高温蒸汽和冷凝水循环交替引入模具的内部管路,以实现模具的快速加热与冷却的成型工艺。蒸汽加热系统最高可使模具表面温度达到160℃。但由于蒸汽相对于水热容较小,升温时间较长。
目前很成熟的技术有日本小野产业株式会社开发的蒸汽加热系统。山东大学海信研究院在高光无熔痕绿色注塑新技术及其成套工艺与装备研究中也取得重要进展,实现了高光液晶平板电视机面板的连续注塑生产。
目前温度控制管理系统还存在一些问题是需要解决。一是实用的加热方法少,比较成功的为蒸汽、高温水加热,二是高光注塑都是采取单独的模具的温度控制管理系统,需要和注塑机配合使用。三是设备及运行成本高。如何能让变模温控制技术在不影响成型周期的每件下进行经济规模生产是大家争相发展与突破的题目。今后需要在实用的低成本快速加热方法、集成的高光注塑机等方面进一步研究开发。
采取电阻加热元件(电热板,电热框,电热圈等)作为热源,其中电热管应用较多,它以金属管为外壳(包括不锈钢、紫铜管),沿管内中心轴向均布螺旋电热合金丝(镍铬、铁铬合金),其空隙填充压实拥有非常良好绝缘导热性能的氧化镁砂,管口两端用硅胶密封。电热元件可加热空气、固体和各种液体。目前直接加装在模具里的电热器加热系统成本比较高,并需支付模具设计专利费。电热管加热速度较快,控制温度范围可达350℃,利用该系统后,15s就可将模具的温度加热到300℃,然后15 s又能将模具的温度冷却到20℃。但只适合尺寸较小的产品使用。由于加热丝直接加热温度比较高,相对模具寿命会缩短。
高光注塑最关键的是模具的温度控制管理系统。由于高光注塑与一般注塑最大不同之处在于模具的温度的控制,而对注塑机的要求并不高。高光注塑模具的温度控制管理系统一般也称为高光模温机,和通用注塑机配合,在注塑的填充、保压、冷却、开合模具过程中协调动作。
模具表面的加热方式是温控系统的关键技术,高光模具表面主要是通过以下方式获得热量。一是以热传导为主的加热方式,如通过模具内部管道的油、水、蒸汽、电热元件等将热量传导到模具表面;二是以热辐射为主的加热方式,如将太阳能、激光束、电子束、红外光、火焰、气体等直接辐射模具表面;三是通过自身热场加热,如通过电阻、电磁感应加热等使模具表面自身产生热量。目前实用的加热系统有:高温油传热的油温机、高温度高压力水传热的高压水温机、蒸汽传热的蒸汽模温机、电热管传热的电热模温机,以及电磁感应加热系统和红外辐射加热系统等。
模温动态控制技术是一种新型绿色注射成型技术。对模温实行动态控制,可以有效消除制品表面熔接痕,减少制品残余应力,获得良好的表面上的质量。本文重点结合实现模温动态控制的快变模温技术原理,介绍了蒸汽加热、电磁加热、红外加热等多种新型加热方式,并展望快变模温技术的发展前景。
模具温度与制品精度、生产效率紧密关联,是当前行业内研究的热点。快变模温技术通过对模温的动态控制,可以有效提升熔体充模流动能力,降低注射压力,改善制品成型工艺;降低注射速率和熔体充模过程中受到的剪切力,减小最终制品的残余应力和翘曲变形,改善制品结构性能。模温的动态变化有效地避免熔体在型腔壁处形成冷凝层,消除制品表面的熔接痕、浮纤等缺陷,使制品表面呈现高光效果。快变模温技术是十分具有发展前途的绿色制造技术。
根据电磁感应原理使工件的温度上升。由于集肤效应,在工件表面上产生的涡流最强,而在内部很弱,到芯部接近于零。因此这种方法可只对工件表面至集肤深度范围加热,因此加热体积小,升温速度快,加热速度在14℃/s以上,如台湾中原大学研发的系统升温速度已达到20℃/s以上。表面加热完成后,再搭配快速低温冷却设备,可达到模具表面快速加热、冷却的效果,实现变模温控制。
模具温度是注塑成型的过程中影响制品质量的重要工艺参数。收缩变形是影响注塑制品最终尺寸精度的重要的条件之一。
影响制品收缩变形的因素包括制品成型的过程中的残余应力、从型腔取出後的分子继续结晶行为以及材料的应力松弛。在注射成型制品时,通过提高模具的温度可有效降品残余应力的产生。同时,高模温还可使制品充分结晶,从而显着降低脱模後收缩量。此外,高模温还可减小制品的冷却速率,使聚合物分子链充分地松弛、恢复,此时制品内应力小,後收缩变形也小。快变模温控制技术与传统模温控制技术相比较,其根本不同之处在于对模具的温度的动态控制。快变模温技术有如下特点: